CO2-Kälteanlagen: Typische Verunreinigungen und wie man sie vermeidet
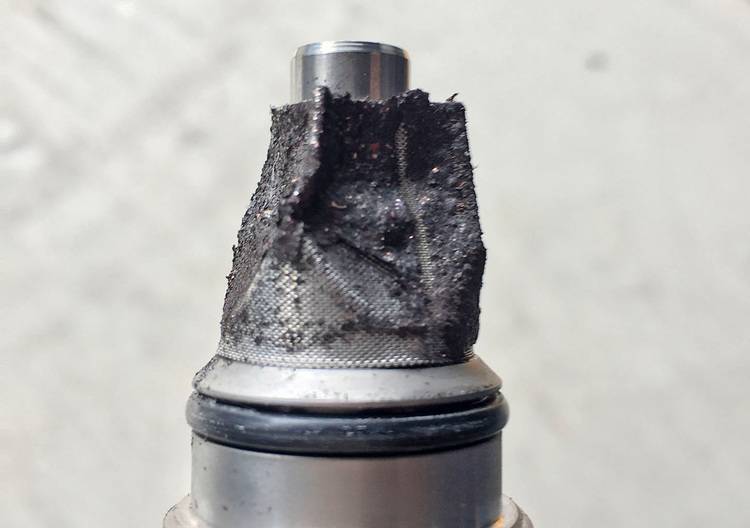
Verunreinigungen an und in Kälteanlagen führen in großem Maße zu Beeinträchtigungen der Funktion, Lebensdauer und Effizienz. Dabei ist es in erster Linie unerheblich, welches Kältemittel zum Einsatz kommt. Allerdings weisen CO2-Anlagen technisch und bauartbedingt Besonderheiten auf. Beispielsweise werden Rohrleitungen und Komponenten deutlich kleiner dimensioniert und es kommen prozessbedingt mehr Regelventile zum Einsatz. Diese und weitere Beispiele zeigen, dass für CO2-Systeme neue Lösungen entwickelt werden mussten. Wir sprachen mit Simon Ahlers, Produktmanager CO2-Systeme bei TEKO Kältetechnik.
Herr Ahlers, welche Verunreinigungen sind in Kälteanlagen immer wieder zu finden und woher kommen sie?
Simon Ahlers: Auf Baustellen ist es nie sauber. Daher ist es besonders wichtig, offene Bauteile vor Staub oder Sand zu schützen. Diese so genannten körnigen Verunreinigungen können bei offener Bauteillagerung in den Kältekreis dringen und Schäden verursachen.
Aus diesem Grund sollten alle offenen Bauteile mit Verschlusskappen verschlossen und vor der Installation mit Stickstoff gereinigt werden. Luftseitige Verschmutzungen wie z.B. Ablagerungen von Staub, Pollen, Laub oder Vereisung an wärmeübertragenden Oberflächen von Gaskühlern und Verdampfern bewirken einen schlechteren Wärmeübergang vom Kältemittel in die Luft oder umgekehrt.
Der schlechtere Wärmeübergang muss dann durch höhere Temperaturdifferenzen ausgeglichen werden. Darunter können das Leistungsvermögen und die Effizienz der Kälteanlage leiden – bis hin zum vollständigen Versagen der gesamten Anlage.
Können Sie die Möglichkeiten der Verunreinigungen spezifizieren?
- Wasser entsteht durch Luftfeuchtigkeit, unverschlossene Bauteile, die Regen ausgesetzt sind, bei der Kühlung von z.B. Lötstellen, bei der Bauteilherstellung aus Kühlschmiermitteln oder Frostschäden an Wärmetauschern.
- Zunder (Metalloxid) entsteht durch Oxidation von Metalloberflächen (z.B. Kupferrohr) bei sehr hohen Temperaturen (z.B. Löten oder Schweißen) und vorhandenem Sauerstoff.
- Durch die Bearbeitung von Bauteilen (z.B. Bohren oder Fräsen, Feilen oder Schleifen) können Metallspäne in den Rohrleitungen verbleiben oder aber auch innerhalb des laufenden Anlagenprozesses entstehen.
- Im laufenden Betrieb von Anlagen kann ein Materialabrieb an allen bewegten Teilen entstehen. Verstärkt wird dieser bei unzureichender Schmierung (z. B. der Kolben oder Ventilsitze). Der Materialabrieb gelangt als Späne, Staub oder Splitter in den Kältekreislauf und kann zum Abrieb weiterer Bauteile oder deren Zerstörung beitragen.
- Bei zu hohen Betriebstemperaturen, z. B. ausgelöst durch hohe Verdichtungsendtemperaturen, entsteht ein chemischer Zersetzungsprozess des Kälteöls – „Ölkohle“. Das führt zu Verstopfungen an Filtern und Ventilen.
- Verschlussstopfen dienen der Vermeidung innerer Verunreinigung von Bauteilen. Werden sie bei der Bauteilinstallation nicht entfernt, kann das zu Verunreinigungen und Schäden innerhalb der Anlage führen.
Was bewirken diese Verunreinigungen im Kältekreislauf einer CO2-Anlage?
Im Vergleich zu chemischen Kältemitteln hat CO2 (R 744) eine deutlich höhere volumetrische Kälteleistung. Speziell im gasförmigen Zustand wird ein erheblich geringeres Volumen an Kältemittel transportiert, um die gleiche Wärmemenge abzuführen. Dadurch werden insbesondere Rohrleitungen, die Kältemittelgas führen, kleiner dimensioniert. Gleiches gilt auch für alle Einbauteile, die aufgrund zur Verfügung stehender Druckdifferenzen teilweise nochmals kleiner dimensioniert werden können/müssen.
In transkritischen CO2-Kälteanlagen werden prozessbedingt mehr Regelventile eingesetzt als in klassischen F-Gas-Kältesystemen bei gleichzeitig kleineren Querschnitten. Vorhandene Verunreinigungen führen unter anderem deshalb zu einer erhöhten Störhäufigkeit, weil Ventilsitze durch Verschmutzungen blockiert werden oder vorgeschaltete Filter verstopfen.
Weiterhin werden in CO2-Anlagen hauptsächlich Ölabscheider eingesetzt, die nach dem Koaleszenz-Prinzip arbeiten. Hierzu wird ein sehr feiner Filter in den Ölabscheider gesetzt, der kleinste Öltröpfchen fängt, sammelt und in den Abscheiderboden abtropfen lässt. Dieser Filter ist um den Faktor 3–4 kleiner als z. B. gängige Saugleitungsfilter, die vor dem Verdichtereintritt platziert werden. Demzufolge sammeln sich selbst kleinste Verunreinigungen in der Ölabscheiderpatrone.
Verschiedene Verunreinigungen reagieren auch chemisch im Kältekreislauf miteinander. So wird die Kombination von Wasser (Restfeuchtigkeit) mit Polyolesther (Schmiermittel im Verdichter) bei ausreichender Reaktionswärme (hohe Verdichtungsendtemperatur) zu Alkohol und Säure. Die Säure greift dann ohne großen Reaktionswärmebedarf die Rohrleitung oder die Verdichterwicklungen an.
Die Lötvariante mit der geringsten Oxidationsbildung ist das Induktivlöten. Hierbei wird ein elektromagnetischer Induktionseffekt zur Wärmeerzeugung genutzt. Dieses Verfahren steht TEKO als Produktionsbetrieb zur Verfügung, ist auf der Baustelle jedoch leider nicht umsetzbar.
Wie lange verbleibt eine Verschmutzung im Kältekreislauf?
Wie lange die Verschmutzung im Kältekreislauf verbleibt, hängt von vielen Umständen ab und lässt sich kaum vorhersagen. Es kann einen langen Zeitraum − also auch Jahre − dauern, bis eine Verschmutzung wieder bereinigt wurde. Regelmäßige Wartungen – beginnend kurz nach der Inbetriebnahme der Anlage – mit Überprüfung der Filter und Reinigung oder Austausch der Filtereinsätze führen zu einer geringeren Störhäufigkeit, einer höheren Effizienz der Kälteanlage, einer verbesserten Haltbarkeit aller Komponenten und insgesamt zu einer höheren Lebensdauer der Anlage.
Welche Auswirkungen hat Schmutz in der Kälteanlage?
Generell entsteht durch Verschmutzungen im Kältekreis ein deutlich höherer Abrieb bei allen bewegten Teilen. Das Verstopfen von Durchlässen und Sieben erhöht die Druckabfälle und hat einen höheren Energiebedarf zur Folge.
Filter und Siebe fangen einen großen Teil der Schmutzpartikel aus dem Kältekreis ab. In Abhängigkeit von der Filterweite und Größe der Schmutzpartikel kann jedoch nicht jeglicher Schmutz aus dem Kältekreis aufgefangen werden. Bei der Aufnahme von Schmutz können sich Filter und Siebe mit der Zeit zusetzen. Dies kann zu erhöhten Druckabfällen, im schlimmsten Fall zum Versagen der Anlagenfunktion führen.
Für den Anlagenbetrieb bedeutet dies, dass durch einen erhöhten Druckabfall die Kälteleistung der Anlage fallen kann. Im Umkehrschluss führt das zu einer Steigerung der Leistungsaufnahme des Systems und damit zu einem erhöhten Stromverbrauch. Diese Effizienzverluste bedeuten für den Betreiber einen wirtschaftlichen Nachteil.
Setzt sich beispielsweise ein Filter in der Flüssigkeitsleitung zu, kann es zu frühzeitigen Expansionen des Kältemittels kommen. Der Verdampfer wird nicht mehr ausreichend mit Flüssigkeit beaufschlagt und eine ausreichende Kühlung bleibt aus.
Ein weiteres mögliches Szenario ist das komplette Versagen der Anlagenfunktion durch zugesetzte Filter und Siebe. Das führt meist zu kostenintensiven Serviceeinsätzen und im schlimmsten Fall zu Warenschäden mit hohen monetären Verlusten.
In unserem Beispielbild „Stark verschmutztes, beschädigtes Sieb“ war der Druckabfall so hoch, dass das Sieb eingedrückt wurde. Eine Funktion des Ventils ist nicht mehr gegeben. Damit Siebe künftig höheren Druckdifferenzen standhalten können, haben wir mit unserem Lieferanten eine verstärkte Form entwickelt.
Ölreguliersysteme: Der feinste Filter in modernen CO2-Kältesystemen ist meist die Koaleszenzpatrone des Ölabscheiders. Daher bleibt an dieser Stelle ein Großteil des Schmutzes hängen. Die durch die Verschmutzung bedingten Druckabfälle können innerhalb der Patrone leicht zum Reißen des Filters führen. Das führt zum Verlust der Abscheidefunktion der Koaleszenzpatrone, und der Schmutz verteilt sich über das Öl in den gesamten Kältekreislauf.
Die Wirkung des Öls an den Schmierstellen (Kolben, Lager, Ventilsitze) wird durch Schmutzpartikel dramatisch beeinträchtigt. Diese erhöhen den Abrieb deutlich, der wiederum Verschmutzung erzeugt. Der Verdichter ist einem deutlich höheren Verschleiß ausgesetzt. Beschädigte Ventilsitze führen dazu, dass Ventile nicht mehr richtig arbeiten.
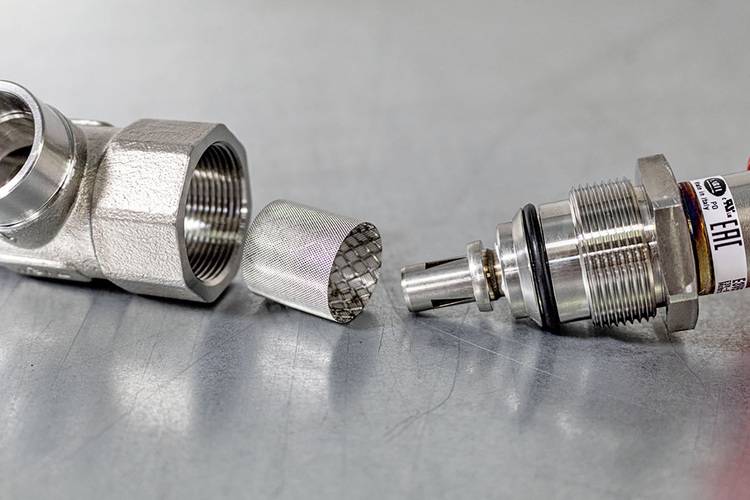
Die Füllung des Kältekreislaufes mit der richtigen Ölmenge ist extrem wichtig. Eine Über- oder Unterfüllung kann zu weiteren Verschmutzungen und Schädigungen innerhalb der Anlage führen. Das Öl benötigt eine bestimmte Zeitspanne, abhängig von Anlagenlaufzeit und Weite des Rohrnetzes, bis es durch den Kreislauf wieder zum Verdichter zurückfließt. Benötigt der Verdichter zu einem Zeitpunkt Schmierung, in dem noch nicht genügend Öl zurücktransportiert wurde, entsteht Materialabrieb innerhalb der Verdichterkolben und Ventilzungen.
Bei einer Überfüllung des Kältekreises kann das Öl schwallweise über die Saugleitung in den Verdichter zurückkommen. Eine zu große Öl-Masse kann der Verdichter nicht verarbeiten. Verdichterausfälle durch Ölschläge sind meist die Folge. Eine hohe Ölmenge an den Wärmetauschern minimiert zusätzlich das Leistungsvermögen der Anlage.
Plattenwärmeübertrager haben sehr kleine Kanäle, die leicht durch Schmutz zugesetzt werden können. Dies kann einen Leistungsabfall der Anlage oder bei kompletter Verstopfung einen Anlagenausfall zur Folge haben.
Ventile: Setzen sich Ventile mit Schmutzpartikeln zu, kann mit der Zeit immer weniger Kältemittel durch die Ventile durchtreten und deren Regelgüte nimmt ab. Bei vollständigem Verschluss hat der Ventilantrieb nicht mehr genügend Kraft, das Ventil zu betätigen.
Das kann einen teilweisen oder kompletten Anlagenausfall zur Folge haben. Beispielsweise bei einem Einspritzventil würde der betroffene Verdampfer ausfallen, die restliche Anlage dagegen weiterlaufen. Es kann aber auch das Gegenteil eintreten. Ventile können durch Schmutzpartikel so beeinträchtigt werden, dass sie nicht mehr richtig schließen.
Ein festsitzendes Expansionsventil birgt die Gefahr von ungewollten internen Leckagen bis hin zu Flüssigkeitsschlägen am Verdichter. Ein nicht schließendes Magnetventil am Ölspiegelregulator kann zur Ölüberfüllung und damit zu Ölschlägen am Verdichter führen.
Wie kann ich eine Verschmutzung erkennen?
Ein guter Indikator zur Feststellung des Verschmutzungsgrades einer Anlage ist die Ansicht und Analyse der Filterpatronen. Schneiden Sie bei einem durchgeführten Wechsel die Filterpatrone auf und begutachten Sie die Siebe. Wir raten dazu, die Siebe zu fotografieren und damit den Grad der Verschmutzung zu dokumentieren. Hat sich nach einem nächsten Wechsel der Grad der Verschmutzung verbessert, nimmt die Verschmutzung in der Anlage ab.
Außerdem sollte man bei jeder Reinigung auch die Prismenschaugläser an Ölspielgelregulatoren und Ölabscheidern kontrollieren! Treten häufig Störmeldungen auf, die das Ölmanagement betreffen, sollte die Anlage umgehend auf den Zustand des Öls kontrolliert werden (Menge/Verschmutzungsgrad).
Ein sicheres Zeichen dafür, dass die Anlage verschmutzt ist, ist die Einfärbung des Öls. Dies ist meist über Ölschaugläser erkennbar. In manchen Fällen sinken die Schmutzpartikel im Öl allerdings ab, sodass eine optische Analyse über die Schaugläser nicht ausreichend ist. Bei einer Wartung empfehlen wir daher, eine Ölprobe am Verdichter zu entnehmen und eine Vergleichsprobe mit frischem Öl durchzuführen.
Wie kann die Verschmutzung einer Kälteanlage möglichst verhindert werden?
Wir empfehlen den Einsatz von Formiergas beim Löten, um unerwünschte Zunderbildung zu vermeiden. Die Filter der Anlage sollten regelmäßig nach der Inbetriebnahme sowie bei jeder Wartung und jedem Serviceeinsatz gewechselt werden. Konkret betrifft das folgende Filter: Koaleszenzpatrone, Filtertrockner, Saugfilter, Ölfilter und Filtersiebe. Zudem sollten die Filter auf den Grad der Verschmutzung kontrolliert werden. Auch im Normalbetrieb der Kälteanlage entsteht Schmutz durch Abrieb. Daher kann auch nach gewechselten Filterpatronen, die sauber waren, immer noch Schmutz entstehen.
Haben Sie Tipps für den Umgang mit Komponenten vor dem Einbau?
Grundsätzlich sollte auf ein sorgfältiges Verschließen aller Bauteile während Lagerung und Transport geachtet werden. Feuchtigkeit und Wasser sind ebenfalls Verschmutzungsfaktoren für eine Anlage. Empfehlenswert ist daher das ordentliche Evakuieren der Anlage vor Inbetriebnahme. Dabei sollte man immer auf den Vakuumdruck achten. Dieser muss deutlich unterhalb der Umgebungstemperatur liegen (siehe Dampfdruckkurve - Grafik unten).
Jegliche Komponenten sollten vor Einbau gereinigt werden. Geschnittene oder gelagerte Rohre sind unbedingt auszupusten, Wärmeübertragerflächen zu reinigen.
Letztendlich ist zu sagen: Verschmutzungen können zu erheblichen Störungen bis hin zu Schäden und Anlagenausfällen führen. Daher sollte grundsätzlich so sauber wie möglich gearbeitet werden. Wichtig ist ebenfalls die regelmäßige Kontrolle des Verschmutzungsgrades während des Anlagenbetriebs, damit man gegebenenfalls eingreifen kann, um die Anlage rund am Laufen zu halten.