Nachhaltiger Beton: Diese Lösungen gibt es bereits
Die Baubranche ist einer der ressourcen- und abfallintensivsten Wirtschaftszweige. Damit nicht genug, ist sie auch einer der größten Treibhausgasemittenten. Hauptursache hierfür ist der hohe Bedarf an Beton. Die Masse des derzeit jährlich weltweit eingesetzten grauen Baustoffs entspricht der Weltnahrungsmittelproduktion im gleichen Zeitraum. Leider ist seine Erzeugung, so wie sie derzeit erfolgt, mit einem hohen CO2-Ausstoß verbunden. Es kommen rund 2,8 Milliarden Jahrestonnen zusammen, die sieben bis acht Prozent der globalen Gesamtemissionen ausmachen. Hinzugerechnet werden müssen die CO2-Emissionen aus der Baustahlerzeugung, rund 50 Prozent der durch die Stahlproduktion insgesamt verursachten drei Milliarden Jahrestonnen.
Wie alle anderen Sektoren, die durch ihren immensen Treibhausgasausstoß die Klimaerhitzung weiter beschleunigen, muss der Bausektor und muss insbesondere die Baustoffproduktion klimaneutral, besser noch: klimapositiv werden, für negative Emissionen sorgen. Ganz besonders gefordert sind die Hersteller von Zement und Beton. Ihre Beschäftigung mit dem CO2-Problem begann in den 1990er Jahren, 2009 wurde eine internationale Roadmap zur CO2-Minderung unter anderem von der IEA vorgelegt, der Internationalen Energieagentur, ergänzt durch Roadmaps einzelner Länder wie China und Indien [1]. 2020 legte die deutsche Zementindustrie eine nationale Roadmap vor, einzelne Zementwerke begannen mit Pilotprojekten [2].
Auf Beton zu verzichten ist dabei keine realistische Option, wie Abb. 1 zeigt. Zementbasierte Baustoffe, ob nun Beton, Mörtel oder Kunststeine, sind als Massenprodukte nicht einfach substituierbar, den Alternativen wie Lehm, Ziegeln oder den hybriden Holzbauten mit hohem mineralischem Baustoffanteil fehlt hierzu das Potenzial. Und wollte man anstatt der weltweit jährlich benötigten 18 Milliarden Tonnen zementhaltiger Baustoffe zum Beispiel konsequent Holz verwenden, wären mehr als 40 Milliarden Kubikmeter davon erforderlich, das Zehnfache der heutigen globalen Holzentnahme [3].
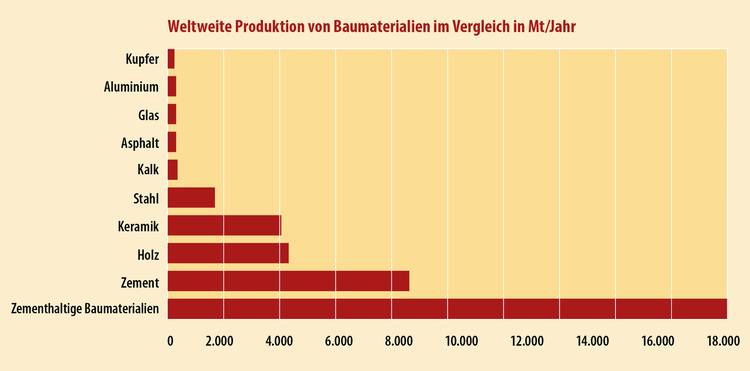
Anfänge in der Antike
Beton ist keine Erfindung der Moderne, bereits die Phönizier nutzten im ersten vorchristlichen Jahrtausend eine Mischung aus gebranntem Kalk und Puzzolan, die unter Wasser abband, ideal zum Bau von Hafenanlagen. Das opus caementitium der Römer geht auf diese Anfänge zurück, ein Material, mit dem unter anderem das Pantheon in Rom gebaut wurde. Mit der heute immer noch größten Kuppel aus reinem Beton, ohne jede Bewehrung, mit einem Durchmesser von gut 44 Metern. Nichtsdestotrotz geriet das Wissen um die Herstellung mit Ende der Antike in Vergessenheit.
Die Wiedererfindung erfolgte im 19. Jahrhundert und sie revolutionierte das Bauen. 1844 entstand der Portlandzement in seiner heutigen Form, durch Brennen eines Mixes aus Kalk und Ton bei hohen Temperaturen, bis zur Sinterung, also fast bis zum Erreichen des Schmelzpunktes. Die nach dem Abkühlen entstandenen Kügelchen, der sogenannte Zementklinker, wurden gemahlen und ergaben ein hochreaktives Pulver. Damit gefertigte Betone, Mörtel und Kunststeine ermöglichten mit ihrer Massenverfügbarkeit das Schaffen von Wohnraum für eine in der Industrialisierung rapide wachsende Bevölkerung. Festigkeit und Feuchte-
unempfindlichkeit des Materials waren die Voraussetzung für sicher gegründete, trockene und solide Häuser mit höherer Geschosszahl sowie für robuste und funktionierende Wasser-, Abwasser- und Verkehrsbauten. Betonbauteile und zementgebundene Baustoffe senkten Baukosten und gewährleisteten nach 1945 durch Vorfertigung den zügigen Wiederaufbau.
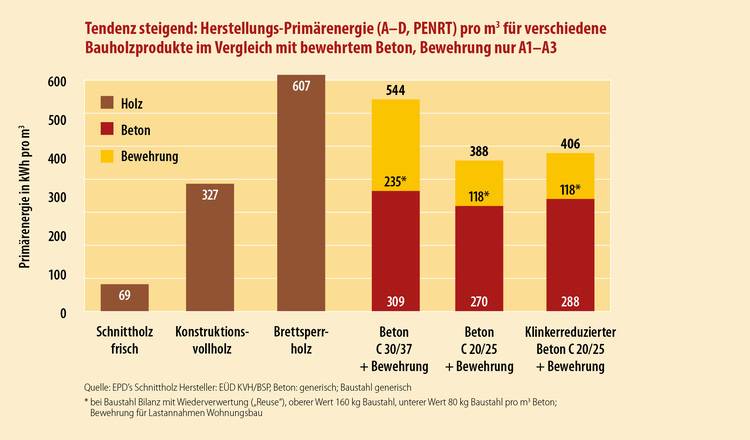
Kohlendioxidquelle Entsäuerung
Die weiter hohe Nachfrage brachte und bringt allerdings auch die besagten hohen Treibhausgasemissionen mit sich. Sie gehen zu einem Drittel auf den Energieverbrauch beim Transport und vor allem beim Brennen des Ausgangsmaterials für den Zement zurück, bei einer Temperatur von 1.450 Grad. Zu zwei Dritteln jedoch entstehen sie bei der dabei erfolgenden „Entsäuerung“ des Kalksteins. Ein weiteres Problem ist der enorme Verbrauch an Zuschlagstoffen wie Sand und Kies. Wüstensand, in beliebiger Menge verfügbar, ist zur Herstellung von Beton nicht geeignet, weil er meist zu feinkörnig und dazu rundgeschliffen ist. Daher ist bei Sand wie auch bei Kies zukünftig Recycling angesagt. Die wichtige Flugasche als Zusatzstoff ist ein Abfallprodukt aus Müllverbrennungsanlagen, aber auch Kohlekraftwerken, und wird damit ebenfalls allmählich knapp.
Den 51 deutschen Zementwerken ist es immerhin gelungen, ihre Emissionen seit 1990 absolut um 25 Prozent und spezifisch, bezogen auf den Zementklinker, um 21 Prozent zu senken, auf insgesamt 20 Millionen Tonnen pro Jahr. Ihr Anteil an den deutschen THG-Emissionen liegt mit nur zwei bis drei Prozent unter dem Weltdurchschnitt; auch bei den spezifischen CO2-Emissionen unterbieten sie den globalen Durchschnitt mit 590 Kilogramm CO2 pro Tonne Zementklinker um 30 Prozent.
CCS und CCU
Um aber die Klimaziele zu erreichen, die Klimaerhitzung abzubremsen und die durch Raubbau fortschreitende Naturzerstörung zu stoppen, muss sich etwas grundlegend ändern. Die Produzenten haben glücklicherweise mehrere Stellen, an denen sie ansetzen können, mehrere Schrauben, an denen sie drehen können. Es zeigt sich jedoch bei näherem Hinsehen, dass nicht alle Wege gleich vielversprechend sind. Offensichtlich keine reelle Lösung ist ein „Weiter so“, ein Festhalten am traditionellen Verfahren zur Herstellung von Zementklinker, bei gleichzeitiger Abscheidung des anfallenden Kohlendioxids. Das dann entweder gelagert wird (CCS = Carbon Capture and Storage) oder sofort für andere Zwecke verwendet (CCU = Carbon Capture and Usage).
Mit der CO2-Abscheidung will die deutsche Zementindustrie jährlich 10 Millionen Tonnen CO2 neutralisieren. Sie setzt damit auf die teuerste Lösung für die Dekarbonisierung des Zements. Vier Projekte sind in der Realisierung. Jedoch wird das Verfahren gerade durch günstigere Techniken überholt. 2017 erarbeiteten 25 Wissenschaftler einen Bericht für die UN Environmental-Programme mit dem Titel: „Eco-efficient cements: Potential economically viable solutions for a low-CO2 cementbased materials industry“, der bereits fortgeschrittenere Methoden und Rezepturen zum Ersatz der kostspieligen CO2-Abscheidung CCS auflisten konnte [4]. Der UN-Bericht kommt zu dem Schluss, „ … dass es mehrere andere mögliche Lösungen gibt, die (…) wesentlich kostengünstiger als CCS erscheinen und das Potenzial haben, einen erheblichen Teil der erforderlichen CO2-Reduktionen zu liefern“ [5].
Die Konzentration auf die Abscheidung des Klimagases entspringt dem Bedürfnis, die kalksteinbasierte Produktionslinie durch klinkerreduzierte Zemente beizubehalten. In der Folge würden pro Zementwerk künftig täglich um die 2.400 Tonnen an flüssigem CO₂ anfallen, das im Rahmen von CCU zum Beispiel zur Härtung von Frischbeton oder zu anderen Nutzungen dienen kann. Im Rahmen von CCS soll das CO2 im Boden unter der Nordsee verpresst werden, was Genehmigungen und Pipelinebauten erfordern würde. Preissteigerungen für Zement um das 2,5-fache sind zu erwarten, die bei CCU durch Erlöse für das CO2 kompensiert werden könnten.
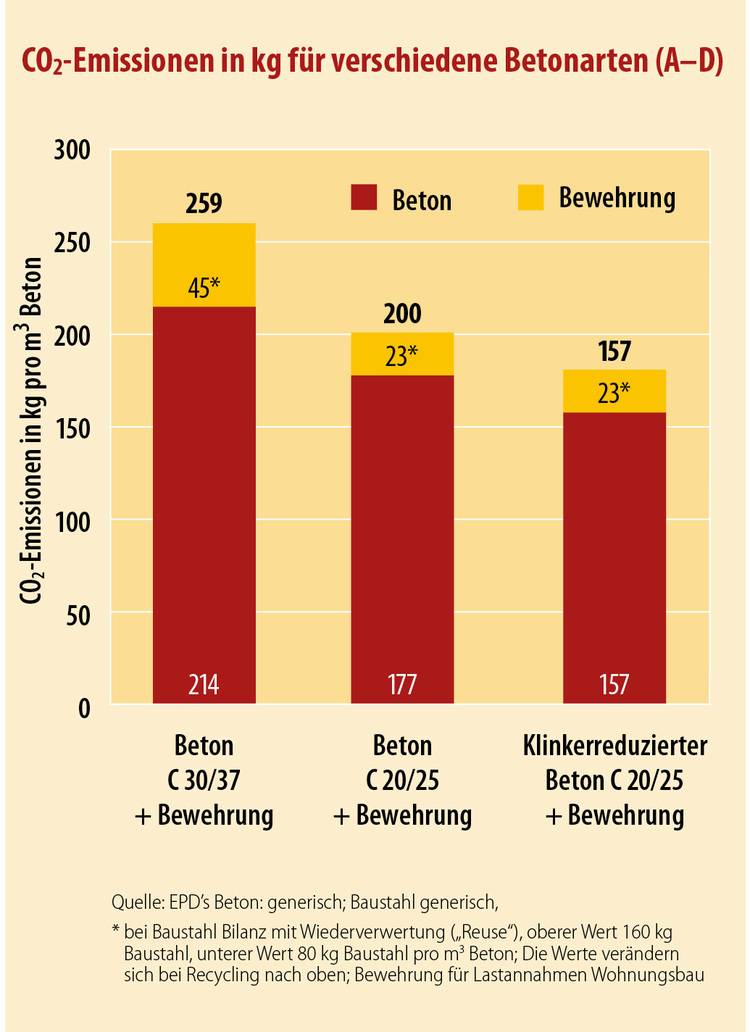
Schlank durch Biodesign
Aus dem Wissen heraus, dass weniger Beton mehr ist, wurden Ideen zur Minimierung des Materialeinsatzes entwickelt. So kommen manche dank neuer Rezepturen hochfeste Betone zum Beispiel mit halb so viel Bewehrungsstahl aus wie konventionelle [6]. Eine weitere Lösung sind Bewehrungen aus dünnen Carbonfasernetzen. Der derart stabilisierte Carbonbeton kann besonders schlank dimensioniert werden, erheblich weniger Zement wird so benötigt. Hierbei ist allerdings noch eine umweltseitige Optimierung der Carbonfaserproduktion erforderlich. Für gering belastete Bauteile sind kurze Polymerstreifen zur Betonbeimischung marktgängig.
Betonkonstruktionen kopieren in ihrer Form immer noch das Gefüge des Holzbaus, aus dem der Massivbau entstand: Träger, Balken, Pfosten. Wesentlich bescheidener ist der Materialeinsatz, lässt man sich im Entwurf von Anfang an von der Natur inspirieren. Beispiele dieses Biodesigns von Gebäuden und Bauteilen gibt es schon vielerorts: Brückenquerschnitte ähneln dann material- und gewichtssparend dem Knochenbau. Eine Reduktion der Betonmengen von bis zu 40 Prozent wurde bereits an einigen Projekten nachgewiesen [7]. Die Herstellung beispielsweise solch innovativer Brückenkonstruktionen kann per 3D-Druck erfolgen. Nach genauer Berechnung der jeweiligen Zug- und Drucklasten in einem Bauwerk können außerdem die Betondichten für die einzelnen Zonen individuell angepasst werden, was gleichfalls eine Materialersparnis bringt.
Auch für den Bau von Windrädern gibt es eine entsprechende, ressourcensparende Methode, nach dem Prinzip der Bionic Technology erdacht und umgesetzt vom Unternehmen Smart & Green Anker Foundations: Rippenelemente als Betonfertigteile ersetzen das bisher vor Ort gegossene Fundament aus gewöhnlich circa 1.300 Kubikmetern armiertem Ortbeton (Abb. 5) . Das mit dem Deutschen Nachhaltigkeitspreis 2023 ausgezeichnete Konzept kommt mit bis zu 70 Prozent weniger Beton beziehungsweise Zement sowie Bewehrungsstahl aus. In Summe beträgt die CO2-Einsparung bis zu 80 Prozent. Die Materialien werden auf Standard-LKW angeliefert (40 LKW anstatt wie bisher 130), innerhalb einer Woche aufgebaut, senken die Baukosten signifikant und erleichtern den Rückbau. Die Wiederverwendung des Fertigteilfundamentes ist möglich. Betoneinsparung durch neues Design wird, ähnlich der Heizenergieeinsparung, eine Dienstleistung von Architekten und Ingenieuren, mit der hier und heute Beiträge zur CO2-Minderung geleistet werden.
Celitement
Neben diesen Möglichkeiten, den Bedarf an konventionellem Beton deutlich zu reduzieren, gibt es jedoch auch zahlreiche Ansätze, die sich mit der eigentlichen Quelle der Emissionen beschäftigen. Das heißt, die den Herstellungsprozess von Beton beziehungsweise Zement umkrempeln. Nach dem Motto „Zement – es kommt darauf an, wie man ihn macht“, in Abwandlung eines bekannten Werbeslogans der Branche aus den 1980ern. Celitement etwa ist ein Bindemittel von Schwenk Zement, hergestellt in einer Karlsruher Pilotanlage. Aktuell laufen Tests auf Baustellen, Weiterverarbeiter arbeiten an ihren Produktlinien. Eine erste industrielle Anlage mit einer Produktionsleistung von 50.000 Jahrestonnen ist geplant. Die Rezeptur des neuartigen Bindemittels basiert auf Kalkstein und Quarzsand, auch Wüstensand ist einsetzbar. Der Kalksteinbedarf ist verglichen mit Portlandzement um circa 30 Prozent geringer. Nach dem Brennen bei nur noch circa 800 Grad Celsius und dem Ablöschen mit Wasser wird der Löschkalk gemeinsam mit Sandschlamm bei circa 200 Grad autoklaviert. Die entstehenden Steine werden in einer speziellen Kugelmühle mechanisch und ohne Wärmezufuhr und CO2-Freisetzung aktiviert. Das finale Produkt bindet bei Wasserzugabe ab und kann vergleichbar eingesetzt werden wie klassische Zemente. Die Herstellung gelingt somit bei niedrigerer Brenntemperatur und die gesamte CO2-Einsparung kann bis zu 50 Prozent betragen. Ein bedeutender Faktor ist die Bereitstellung von Ökostrom aus dem öffentlichen Netz. Neben der CO2-Reduktion weist Celitement weitere Vorteile auf, wie zum Beispiel eine weiße Farbe und eine Verträglichkeit mit regionalen und rezyklierten Gesteinskörnungen.
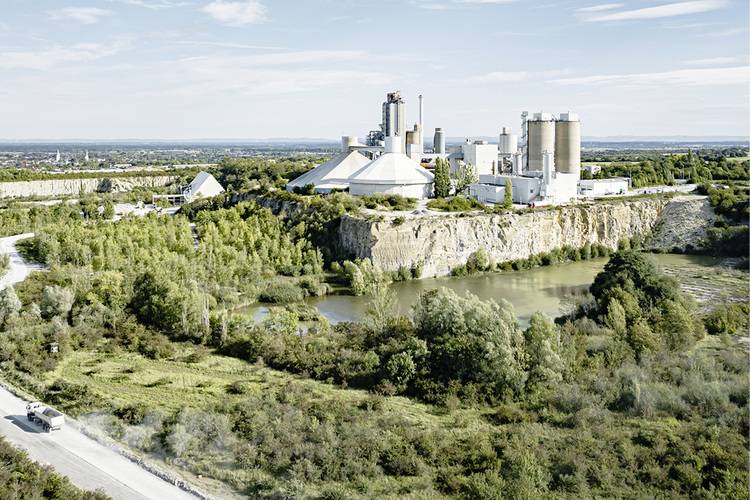
CarbonCure
CarbonCure, ein kanadischer Anbieter, wirbt mit einem hochbelastbaren Endprodukt mit verringertem Zementanteil. Aus der Abscheidung stammendes CO2 ersetzt das Wasser zur Härtung von Beton, Betonsteinen und Mörtel. Das flüssige Kohlendioxid verbindet sich mit dem Material und verbleibt dort dauerhaft. Bei gleichem Preis und gleicher Leistung ist eine Emissionsreduktion von bis zu 50 Prozent möglich. Das Unternehmen ist darüber hinaus mit transportablen CO2-Speichern auch im Bereich Transportbeton engagiert: Das Härten durch die Zugabe von Kohlendioxid findet direkt auf der Baustelle statt.
C-Crete
C-Crete, in den USA entwickelt, wird für Fertigbetonanwendungen genutzt und kommt gänzlich ohne Kalkstein aus. Grundbestandteil des verwendeten Zements ist Zeolith, das durch Wärmebehandlung zum Bindemittel wird. Da kein CO2 durch Kalkbrennen bei der Herstellung entsteht, wird der Zeolith-Beton durch die verbleibende Karbonatisierung über seine Lebensdauer CO2-negativ. In der Nähe der Rohstoffvorkommen besteht Preisgleichheit zu Portlandzement. C-Crete oder künftige europäische Produkte auf Zeolithbasis werden zu den regionalen Angeboten zählen. Deutschland hat keine ausreichenden Ressourcen, dafür existiert jedoch in der Nachbarschaft, in Tschechien, eine Zeolith-Lagerstätte mit Zementwerk.
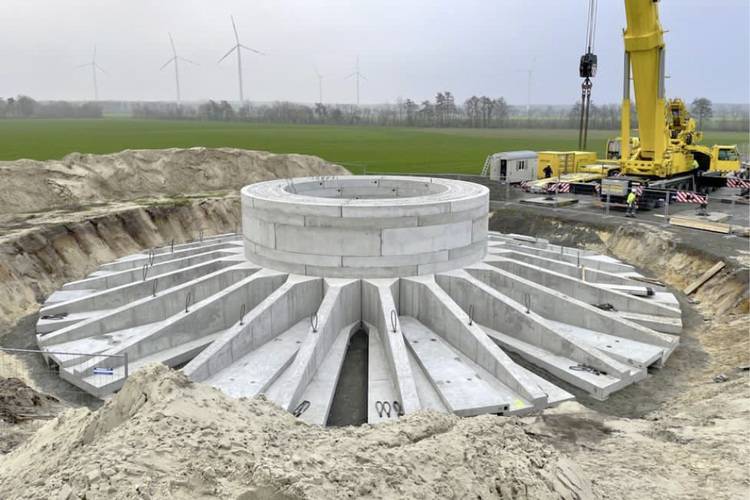
Solidia
Zum Gamechanger könnte der von Lafarge vermarktete Zement der Firma Solidia werden. Er ist korrigierbar und kann bei der Produktion von Betonfertigteilen die CO2-Emissionen um 50 bis 70 Prozent vermindern.
Die Zutaten sind die gleichen wie bei Portlandzement, es wird jedoch weniger Kalkstein eingesetzt und das Brennen erfolgt bei niedrigeren Temperaturen. Der Beton härtet nicht unter Zugabe von Wasser aus, sondern mittels Beimengung von Oxalsäure oder Zitronensäure, die Kooperationspartner des Unternehmens aus industriell abgeschiedenem CO2 herstellen. Der Zement von Solidia emittiert unterm Strich keine Kohlenstoffatome mehr, sondern bindet sie, bis zu fünf Atome pro zwei Calciumatomen. Damit würde Zement zu einer bedeutenden Netto-Kohlenstoffsenke [8]. Er kann darüber hinaus sogar zu niedrigeren Kosten produziert werden als Portlandzement, bei besseren Eigenschaften.
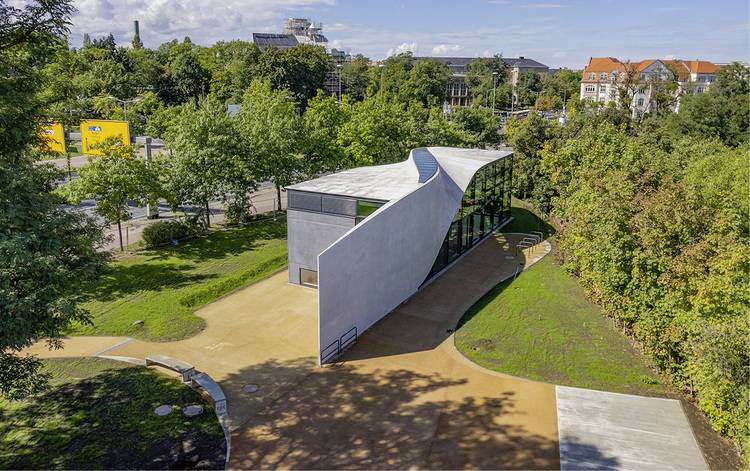
Abbruchmaterial als Rohstoffquelle
Abgesehen vom bewussten, sparsamen Umgang mit den natürlichen Ressourcen kann man noch auf andere Art dafür sorgen, dass der Nachschub an Beton nicht abreißt: durch Nutzung von Recyclaten als Zuschlagstoffen im großen Stil. Die stecken jedoch noch im Altbeton, im Betonschutt auf den Deponien, und sind bisher nur mit erheblichem Aufwand wiederzugewinnen. Im Fraunhofer-Institut für Bauphysik IBP reift jedoch schon seit längerem in aller Stille ein relevanter Teil der Lösung für ein künftiges Recyclingverfahren heran. Eine erste industrielle Anlage mit einer Stundenleistung von drei Tonnen wird gerade projektiert.
Mit der hier durchgeführten elektrodynamischen Fragmentierung kann nicht nur Beton umweltschonend und lärmarm in seine Ausgangsbestandteile zerlegt werden, sondern auch Schlacke aus der Müllverbrennung (Abb. 9). Die elektrischen Impulse in der Anlage zertrümmern das in Wasser liegende Material in wenigen Sekunden. Ausgesiebt gehen die sortenrein getrennten Materialbestandteile wie Sand und Kies wieder in die Produktion (Abb. 10.) Das Verfahren besitzt mehrere bahnbrechende Bestandteile: Es benötigt mit 2,3 Kilowattstunden pro Tonne Abbruchmaterial kaum Energie, nicht einmal Starkstrom, und es macht den Recyclingprozess profitabel. Sein Clou: Beim Durchschlag der ultrakurzen Blitze (< 200 nsec) wird das Bindemittel Zementstein karbonatisiert, schon nach wenigen Minuten wird mengenmäßig das einst beim Brennen des Kalksteins ausgetriebene CO2 wieder im sekundär gebildeten Kalk gebunden. Mit dieser Technologie und der Verwendung von sekundärem Kalk kann die Zementherstellung CO2-neutral werden. Sand und Kies werden einer Kreislaufnutzung zugeführt, die natürlichen Lagerstätten werden entlastet, zusätzlich entstehen kaufmännisch veräußerbare CO2-Emissionsrechte. (Die Kanadier von CarbonCure lassen zerkleinerten Abbruchbeton Kohlendioxid aufnehmen, ein langsamer Prozess der Karbonatisierung, und verkaufen der Softwarebranche die sich so ergebenden „Verschmutzungsrechte“.)
Volker Thome vom Fraunhofer IBP sagt zu den Chancen des Verfahrens: „Die Fragmentierung löst viele Probleme des Recyclings, Sand, Kies und CO2-arme Zementersatzrohstoffe können zurückgewonnen werden. Wir stehen am Anfang einer technischen Revolution im Beton-Recycling, es müssen jedoch auch die politisch-wirtschaftlichen Rahmenbedingungen geschaffen werden, damit das Recycling von Altbeton lohnenswerter ist als eine Deponierung.“
Rege Innovationstätigkeit
Die beschriebenen Verfahren und Techniken können den CO2-Ausstoß in der Betonherstellung drastisch verringern, auf 0 bringen oder den Baustoff sogar klimapositiv machen. Allerdings werden sie den Stromverbrauch erhöhen. Es ist von einem Mehrbedarf von 20 Terawattstunden pro Jahr auszugehen, darin eingeschlossen sind die Verbräuche der künftigen Transportbeton-E-LKWs. Eine der Erfolgsvoraussetzungen ist daher die parallele Dekarbonisierung der Stromerzeugung in Deutschland, mit sinkenden Gestehungskosten, bis herab zu zwei Cent pro Kilowattstunde.
Adrian Zimmermann, Produktentwickler bei Celitement, ist optimistisch, was den Weg hin zu einem nachhaltigen Beton angeht: „Die deutsche Zementindustrie investiert derzeit stärker in Lösungen zur Reduzierung der CO2-Emission als jemals zuvor. Nicht nur anlagentechnische, sondern auch stoffliche Innovationen werden mit Hochdruck vorangetrieben.“ Auf seiner Website gibt das Unternehmen einen Überblick über die Vielfalt der Ansätze in der Branche [9]. Man kann sagen: Die mineralische Bauwirtschaft hat aktuell die Chance, sich selber und – mit Zement und Beton – ihr wichtigstes, massenhaft eingesetztes Material wieder einmal neu zu erfinden. Nicht alle, aber viele ihrer Vertreter nutzen sie.
Der Autor Werner Eicke-Hennig studierte nach einer Bauzeichnerlehre Stadtplanung in Kassel, wo er ab 1984 eine unabhängige Energieberatungsstelle aufbaute. Er war seit 1989 wissenschaftlicher Mitarbeiter am Institut Wohnen und Umwelt (IWU) und dort Leiter der Hessischen Energiespar-Aktion des Hessischen Wirtschaftsministeriums. Seit 2017 ist er im Ruhestand und betreibt das Energieinstitut Hessen in Frankfurt/Main.
Quellen
[1] https://celitement.de/roadsmaps-berichte/
[2] Verein Deutscher Zementwerke, VDZ, Hrsg. Dekarbonisierung von Zement und Beton – Minderungspfade und Handlungsstrategien. Düsseldorf, 2020
[3] UN Environmental-Programme, „Eco-efficient cements: Potential economically viable solutions for a low-CO2 cement-based materials industry“, Paris 2017
[4] UN Environmental-Programme, ebenda
[5] UN Environmental-Programme, ebenda
[6] Amory B. Lovins, Profitably Decarbonizing Heavy Transport and Industrial Heat: Transforming These “Harder-to-Abate” Sectors Is Not Uniquely Hard and Can Be Lucrative, 2021, https://www.rmi.org/profitable-decarb/
[7] Amory B. Lovins, Profitably Decarbonizing Heavy Transport and Industrial Heat, ebenda
[8] ebenda
Daten Zementindustrie Deutschland
- 51 Zementwerke mit 49 Zementdrehöfen
- 34 Mio. Tonnen Zementproduktion pro Jahr
- 27,5 Mio. Tonnen Zementverbrauch pro Jahr
- Wärmeverbrauch der Werke 26,7 TWh, davon nur noch 1/3 durch Kohle
- 20 Mio. Tonnen CO2eq-Emissionen pro Jahr
- 587 kg CO2eq-Emissionen pro Tonne Zement
- Ressourceneinsatz in Mio. Jahrestonnen: Kalkstein 38; Ton 1,2; Sand 1,1; Hüttensand 7,7; Flugasche 0,3
- Klinkeranteil am Zement 70-80 %
- CO2-Entstehung: 40 % durch Feuerung, 60 % durch Umwandlung des Kalksteins zu Brandkalk
- 84 % des Zements gehen in 1.870 Transportbeton- und Fertigteilwerke, nur 6 % sind Sackzement
- Transportbeton: 52,2 Mio. m³ pro Jahr
- 33 % des Betoneinsatzes im Wohnungsbau
- 34,4 % des Betoneinsatzes im Nichtwohnungsbau
- 32,6 % im Tiefbau einschließlich Straßenbau